
Un nuevo material mejora los implantes de cartílago para la rodilla
Un equipo internacional de investigadores, con participación de la Universidad Politécnica de Valencia, ha desarrollado un material polimérico que mejora la calidad y resistencia de los implantes de cartílago articular en operaciones de rodilla. De esta forma aumenta su durabilidad hasta en un 80% respecto a los que se usan actualmente.
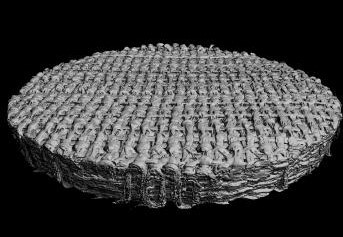
Estructura del nuevo material observado con un microtomógrafo de rayos X. / UPV
El desgaste del cartílago es una de las lesiones que más afecta a deportistas como corredores, tenistas, jugadores de pádel y, en general, a todos aquellos que practican algún deporte de alto impacto para las articulaciones. La solución a esta patología pasa, en muchas ocasiones, por una intervención quirúrgica, en la que el cartílago dañado se sustituye por un polímero 3D, cuyas prestaciones mecánicas son muy parecidas a la del tejido natural.
Con el nuevo material los implantes podrían durar hasta un 80% más que los utilizados actualmente
Este tejido ha de tener la suficiente porosidad para que el hueso y capilares puedan crecer en su interior. Sin embargo, diferentes estudios realizados sobre este tipo de materiales constatan cómo su resistencia, con el paso del tiempo, es deficiente.
Ahora investigadores de la Universidad Politécnica de Valéncia, la Universidad de Notre Dame (EE UU) y la Universidad Tecnológica de Auckland (Nueva Zelanda), junto con la multinacional Zimmer, han desarrollado un nuevo material que mejora la calidad y durabilidad de los implantes de cartílago articular en las operaciones de rodilla. Los detalles los publican en la revista Materials Science and Engineering.
“La utilización del material que hemos obtenido permitirá incrementar la vida útil de estos implantes, con el consiguiente beneficio para el paciente”, destacan los profesores Miguel Ángel Sellés y Samuel Sánchez, profesores del Campus d’Alcoi e investigadores del Instituto de Tecnología de Materiales y del Instituto de Diseño y Fabricación de la UPV, respectivamente. Según las pruebas que han llevado a cabo, con el nuevo material los implantes podrían durar hasta un 80% más que los utilizados actualmente.
Tecnología láser para obtener tejido soldado
Para la obtención de este material –se trata del primer tejido soldado aplicado al sector– los investigadores han desarrollado una nueva técnica, basada en el uso de tecnología láser.
“En nuestro estudio observamos que para evitar el desgaste del cartílago, resulta fundamental que las fibras no se desvíen lateralmente cuando están sometidas a una carga normal, entendiéndose como tal una fuerza perpendicular a la superficie exterior del implante. Para ello, proponemos un método basado en la soldadura selectiva por láser de las capas superficiales de los tejidos tridimensionales”, explica Sellés.
La técnica utilizada va impregnando las fibras del tejido polimérico por capas en una solución que permite que el material absorba con eficacia la energía del haz láser y que las fibras se unan entre sí en puntos muy localizados. De esta forma, las fibras son más fuertes y el material es mucho más resistente.
“Los resultados de los estudios tanto del método de fabricación de tejidos 3D como del propio material han sido excelentes. Las tasas de desgaste se redujeron significativamente y la vida útil del implante se incrementó notablemente gracias a la soldadura en superficie, lo que hace que esta sea una opción viable para el reemplazo de cartílago in vivo”, apunta Sánchez.
Referencia bibliográfica:
lT.Rodts, S.R.Schmid, M.A.Selles, T.Pasang S.Sanchez-Caballero. "Selective laser fiber welding on woven polymer fabrics for biomedical applications". Materials Science and Engineering, enero de 2019. https://doi.org/10.1016/j.msec.2018.10.018
No hay comentarios:
Publicar un comentario